MANUFACTURING MODULAR OPERATION THEATER
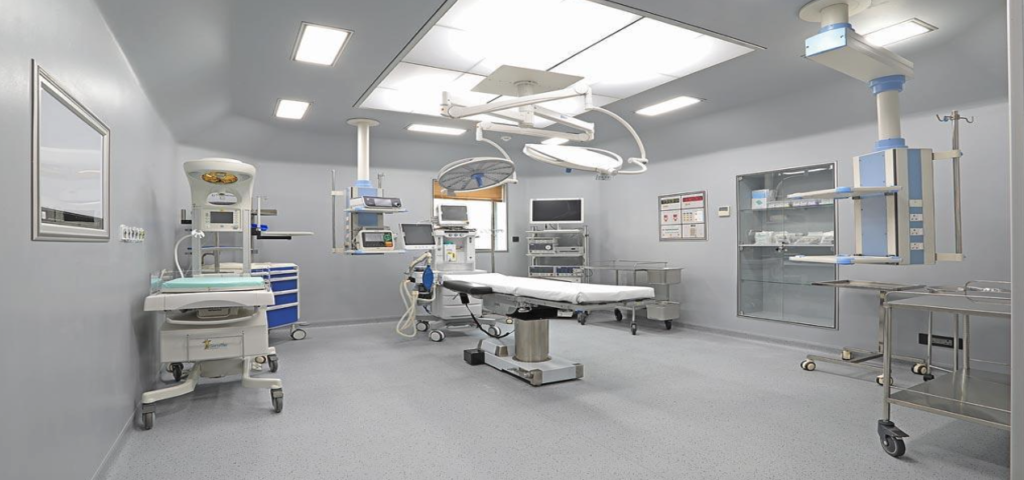
Manufacturing a modular operation theater involves several steps and considerations. Here’s a general outline of the process:
Planning and Design:
- Identify the specific requirements and functional aspects of the modular operation theater (OT).
- Determine the dimensions, layout, and configuration based on the available space and intended use.
- Collaborate with architects, engineers, and healthcare professionals to design an OT that meets regulatory standards and ensures optimal workflow.
Material Procurement:
- Source high-quality materials and equipment required for constructing the modular OT, such as structural components, wall panels, flooring, lighting fixtures, HVAC systems, medical gas systems, and electrical fittings.
- Ensure that the materials meet the necessary safety and regulatory standards.
Construction of Modules:
- Construct the modular components of the OT off-site in a controlled manufacturing facility.
- Build individual modules such as walls, floors, ceilings, and utility service units using pre-fabricated materials.
- Install necessary electrical wiring, plumbing, medical gas pipelines, and HVAC systems within the modules.
- Test and inspect each module to ensure compliance with safety and quality standards.
Transportation and Assembly:
- Transport the pre-fabricated modules to the final installation site.
- Prepare the foundation and infrastructure required for the OT.
- Assemble the modules on-site according to the predetermined layout and design.
- Connect utilities, including electrical, plumbing, medical gas, and HVAC systems, between the modules.
- Perform thorough inspections and testing of the assembled OT to ensure functionality, safety, and compliance.
Finishing and Integration:
- Install necessary finishes, such as wall coverings, flooring, lighting fixtures, and doors.
- Integrate medical equipment, surgical tools, monitors, and other necessary technology into the OT.
- Ensure proper integration of communication systems, data networks, and audiovisual equipment.
- Conduct final checks and inspections to verify that all components are in working order and meet the required standards.
Certification and Commissioning:
- Collaborate with relevant regulatory authorities to obtain necessary certifications and clearances for the modular OT.
- Conduct final inspections and tests to ensure compliance with applicable healthcare standards and guidelines.
- Train healthcare personnel on the proper use of the modular OT and its equipment.
- Obtain operational clearance and necessary permits for the OT’s use.
Remember that the specific details and requirements for manufacturing a modular OT may vary depending on local regulations, healthcare standards, and project-specific needs. It is crucial to involve experienced professionals and consult with relevant authorities throughout the process to ensure a safe and compliant operating environment.